Pipe Flange Types in Industrial Piping Systems
Flanges play a critical role in industrial piping systems, providing a secure and reliable method for connecting pipe, valves, and other equipment. As essential components in well drilling, aviation fueling, sanitary, and structural applications, flanges must be designed to withstand high pressures, extreme temperatures, and corrosive environments.
At Cole Industrial, we offer a wide selection of high-quality flanges that meet the demands of various industries. Understanding the different types of flanges available is essential to selecting the right one for your specific application. Below, we provide a detailed overview of the different flanges available at Cole Industrial and how they are used in industrial operations.
Weld Neck Flanges
Weld neck flanges are one of the most durable and reliable flange types available. They feature a long tapered hub that provides reinforcement in high-pressure environments, reducing stress concentration and increasing structural integrity. This design makes them ideal for applications that experience high temperatures and extreme pressure fluctuations.
Industries such as oil and gas, petrochemical, and power generation frequently utilize weld neck flanges due to their ability to maintain a secure connection even under severe conditions. The installation process involves butt welding the flange to the pipe, creating a strong and leak-resistant joint. While weld neck flanges require more labor-intensive installation compared to other flange types, their long-term performance and reliability make them an excellent investment for critical applications.
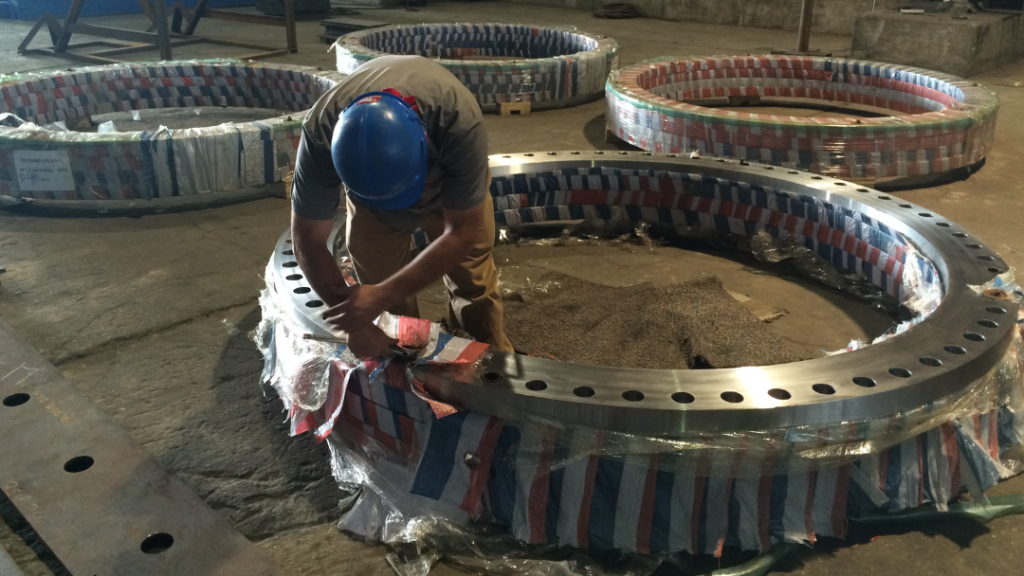
Slip-On Flanges
Slip-on flanges are a popular choice for low-pressure applications where ease of installation is a priority. These flanges slide over the end of a pipe and are then welded into place. Their simple design and cost-effectiveness make them a common choice for industries such as water treatment, HVAC, and low-pressure chemical processing.
Although slip-on flanges are easier to install than weld neck flanges, they provide less structural integrity and are not recommended for high-pressure or high-temperature environments. However, their ease of alignment and lower initial cost make them a practical option for applications that do not require extreme durability.
Blind Flanges
Blind flanges serve a unique function in industrial piping systems by sealing the end of a pipe, preventing the flow of fluids or gases. These flanges are commonly used in systems that may require future expansion or modification, as they allow for easy access when needed.
Blind flanges are often used in industries such as oil and gas, chemical processing, and power generation. They are designed to withstand high pressure and provide a secure seal, ensuring that the piping system remains leak-free. The thickness and material of the blind flange must be carefully selected based on the specific operating conditions to ensure long-term durability and performance.
Threaded Flanges
Threaded flanges, also known as screwed flanges, are designed for applications where welding is not feasible or practical. These flanges have internal threads that match the external threads of the pipe, allowing for a secure and tight connection without the need for welding.
Industries that require quick installation and removal, such as plumbing and low-pressure gas distribution, often utilize threaded flanges. While they provide convenience, threaded flanges are not suitable for high-pressure or high-temperature applications due to the risk of thread wear and leakage over time. However, in low-pressure systems, they offer a reliable and efficient connection method.
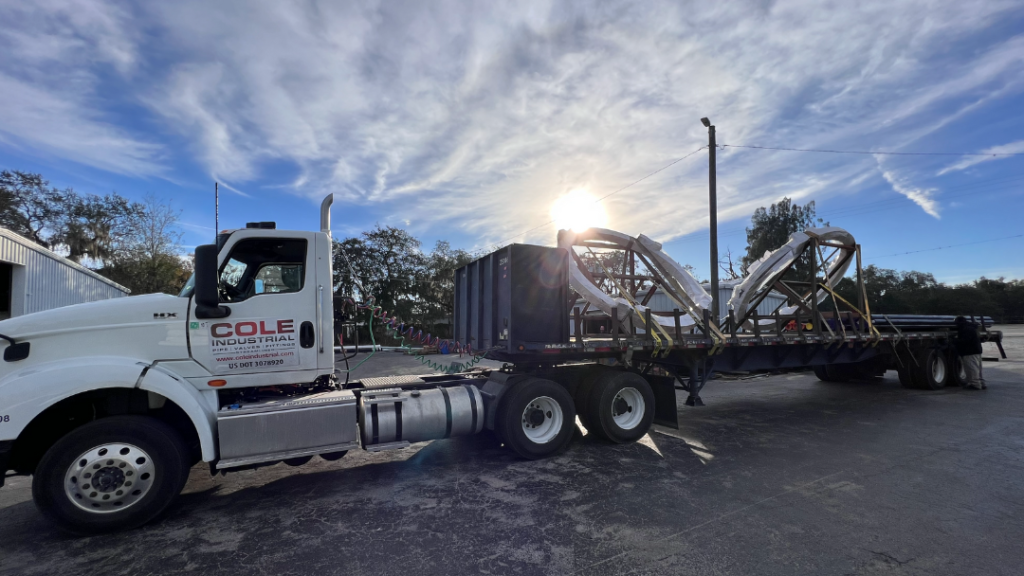
Socket Weld Flanges
Socket weld flanges are designed for small-diameter, high-pressure piping systems. They feature a socket-like cavity where the pipe is inserted before being welded at the connection point. This design creates a strong and leak-resistant joint while minimizing turbulence and stress at the weld site.
Commonly used in chemical processing, hydraulic systems, and high-pressure steam applications, socket weld flanges provide excellent performance in demanding environments. Their compact design makes them ideal for systems where space is limited, and their high-strength connection ensures reliability under pressure.
Lap Joint Pipe Flanges
Lap joint flanges are typically used in systems that require frequent dismantling for inspection, cleaning, or maintenance. These flanges consist of two components: the stub end, which is welded to the pipe, and the lap joint flange, which is free to rotate around the stub end.
This design allows for easy alignment and installation, making lap joint flanges a preferred choice in industries such as food processing, pharmaceuticals, and water treatment. While they are not as strong as other flange types due to the absence of a direct weld connection, they offer flexibility and ease of use in applications where alignment and maintenance are a priority.
Orifice Flanges
Orifice flanges are specially designed for flow measurement applications. They contain drilled holes that allow for the installation of an orifice plate, which measures the flow rate of fluids within a pipeline. These flanges are commonly used in the oil and gas, chemical processing, and power generation industries where accurate flow measurement is essential for operational efficiency.
Orifice flanges are designed to handle high-pressure environments and are available in various sizes and materials to accommodate different flow measurement requirements. Their precision and reliability make them an integral part of process control and monitoring systems.
Expanding and Reducing Flanges
Expanding and reducing flanges provide a solution for connecting pipes of different diameters. Expanding flanges gradually increase the diameter of a pipeline, while reducing flanges decrease it. These flanges are used in applications where system modifications require a change in pipe size without extensive reconfiguration.
Industries such as wastewater treatment, chemical processing, and industrial manufacturing benefit from the adaptability of expanding and reducing flanges. They provide a secure and leak-free transition between different pipe sizes, ensuring efficient flow management.
Choosing the Right Pipe Flange for Your Application
Selecting the right flange type depends on various factors, including pressure and temperature conditions, installation requirements, and the need for future maintenance.
Each flange type serves a specific purpose, and understanding these differences can help ensure optimal performance and longevity in industrial piping systems.
At Cole Industrial, we are committed to providing high-quality flanges that meet the needs of diverse industries.
Our extensive selection includes weld neck, slip-on, blind, threaded, socket weld, lap joint, orifice, expanding, and reducing flanges, ensuring that our customers have access to the right products for their specific applications.
Trust Cole Industrial for Your Pipe Flange Needs
With years of experience in the industrial supply industry, Cole Industrial is a trusted partner for high-quality flanges and piping components.
Our expertise in well drilling, aviation fueling, sanitary, and structural applications allows us to provide tailored solutions that meet the unique demands of our customers.
Whether you need durable weld neck flanges for high-pressure environments or flexible lap joint flanges for frequent maintenance access, Cole Industrial has the inventory and knowledge to support your project.
Contact us today to learn more about our flange offerings and how we can help you achieve reliable, efficient piping system performance.